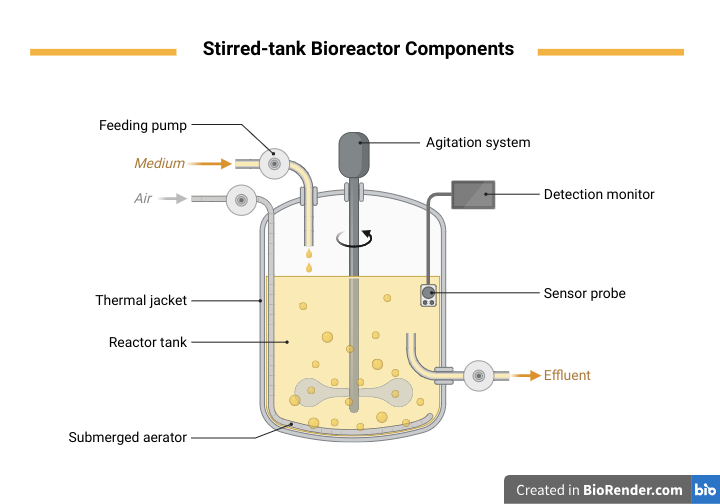
Key components of bioreactors
A bioreactor is a controlled environment used for the cultivation of microorganisms, cells, or tissues. It consists of several key components that work together to provide the necessary conditions for cell growth and product formation.
Here are the key components of a bioreactor:
Vessel or chamber
The vessel is the main container where cell culture or microbial fermentation takes place. It is typically made of stainless steel or glass and is designed to be sterile and airtight to prevent contamination and maintain controlled conditions.
Agitator or stirrer
The agitator is a mechanical component that mixes the contents of the vessel. It ensures uniform distribution of nutrients, oxygen, and temperature throughout the culture. Common types include impellers and paddles.
Heat exchanger
A heat exchanger is used to control the temperature inside the bioreactor. It can heat or cool the culture medium as needed to maintain the desired temperature for cell growth or fermentation.
pH control system
This system measures the pH level of the culture and adds acid or base as necessary to maintain the pH within a specified range. Consistent pH control is crucial for cell viability and product yield.
Aeration and gas supply
Bioreactors provide oxygen to the culture through aeration or sparging. Aeration systems can include spargers, diffusers, or bubblers to deliver oxygen and remove carbon dioxide produced during metabolism.
Nutrient inlet-outlet
Nutrients, such as sugars, salts, vitamins, and trace elements, are added to the bioreactor through an inlet. Waste products are removed through an outlet to maintain a balanced culture medium.
Sensors and analytical instruments
Various sensors are integrated into the bioreactor to monitor parameters like temperature, pH, dissolved oxygen, and biomass concentration. These sensors provide real-time data for process control and optimization.
Sampling ports
Sampling ports allow researchers to collect samples of the culture for analysis without disturbing the entire process. Sampling is essential for assessing cell density, product concentration, and other parameters.
Control system
The control system manages and regulates the bioreactor’s operating conditions based on input from sensors. It controls temperature, pH, oxygen levels, agitation speed, and nutrient addition to maintain optimal culture conditions.
Sterilization system
To ensure aseptic conditions, bioreactors have a sterilization system that can use methods such as autoclaving, chemical sterilization, or in-place sterilization of components.
Sparger or air inlet
The sparger is a component that introduces air or oxygen into the culture medium. It may be a porous tube or diffuser that creates small bubbles for efficient oxygen transfer to the cells.
Foam control system
Agitation and aeration can produce foam on the surface of the culture. Foam control systems prevent excessive foam buildup, which can interfere with culture conditions and lead to contamination.
References
1. Lim D, Renteria ES, Sime DS, Ju YM, Kim JH, Criswell T, Shupe TD, Atala A, Marini FC, Gurcan MN, Soker S, Hunsberger J, Yoo JJ. Bioreactor design and validation for manufacturing strategies in tissue engineering. Biodes Manuf. 2022 Jan;5(1):43-63. doi: 10.1007/s42242-021-00154-3. Epub 2021 Jul 19. PMID: 35223131; PMCID: PMC8870603.
2. Selden C, Fuller B. Role of Bioreactor Technology in Tissue Engineering for Clinical Use and Therapeutic Target Design. Bioengineering (Basel). 2018 Apr 24;5(2):32. doi: 10.3390/bioengineering5020032. PMID: 29695077; PMCID: PMC6027481.
3. Stephenson M, Grayson W. Recent advances in bioreactors for cell-based therapies. F1000Res. 2018 Apr 30;7:F1000 Faculty Rev-517. doi: 10.12688/f1000research.12533.1. PMID: 29770207; PMCID: PMC5931275.
4. https://microbiologynote.com/bioreactor/